PhD Theses
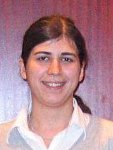
Anamaria DOGAR
Title: Advanced Techniques of Image Processing for Optimization of Assisted Quality Control
Supervisor: Professor Theodor BORANGIU
Final presentation in 2009
The quest for agility and re-configurability requires a new class of production control systems, characterized by: (i) a set of distributed, autonomous and intelligent building blocks, designated as control units; (ii) autonomy of each control unit which has its own objectives, knowledge and skills; (iii) global decisions are obtained by the cooperation of more than one control unit; (iv) control units adapt to changes without external intervention; (v) control units of mechatronic devices such as machine tools, robots, conveyors and vision sensors, are part of reconfigurable, fault-tolerant planning, control and test architecture of global manufacturing system; (vi) input data and formats for part processing are subject to increased diversity, requiring both high-speed cooperation between external sensors (range finder, machine vision), intelligent robots and CNC machine tools, and easy reconfigurable, task-driven software systems capable to detect, recognize, locate, qualify, inspect complex objects and accurately represent in digital form their 2D/3D surfaces/shapes.
This thesis presents an integrated quality control system for manufacturing industry. The proposed system combines several components in order to provide an efficient solution for complex real-time measurements tasks: image processing system which can be adapted to specific requirements, monochrome video cameras and a laser scanner probe, all integrated in a flexible manufacturing cell. Standard visual inspection tasks are performed by the 2D vision system. Due the increased complexity of inspection applications, standard procedures do not always suffice to achieve given quality standards. The quality control system provides the 3D solution by integrating a 6 d.o.f. robot mounted laser scanning device.
Thus, the extension of traditional material-handling control to material-conditioning functions, allows the relaxation of material flow and process constraints imposed to the transportation means, as well as on line integration of quality control in the global manufacturing system. This functional extension becomes possible in the proposed robot-vision architecture by taking over: (i) the powerful description of material flows through an efficient set of form-, surface-, and pose features of circulating parts, based on real-time, high-speed image processing and (ii) applying Artificial Intelligence concepts to reach a global autonomous, self-learning, task- and context-dependent behavior of the robotized manufacturing system with adaptation to the working environment.